Introduction
Building a house is a significant undertaking, and one of the most critical aspects of the construction process is determining how much lumber you’ll need. Whether you’re a homeowner planning to build your dream home or a contractor working on a project, understanding the lumber requirements for a 1500 square foot house is crucial. In this article, we will break down the various factors that influence the amount of lumber needed, helping you make informed decisions and manage your construction budget effectively.
The Importance of Proper Planning
Assessing the Design
Before you can calculate the exact amount of lumber required, you must assess the design of your house. The architectural style, number of rooms, and unique features will all impact the lumber needs.
Understanding Local Building Codes
Local building codes and regulations dictate specific requirements for structural support and safety. Ensure you are familiar with these codes to determine the necessary lumber sizes and types.
Calculating Lumber for Framing
Wall Framing
The walls are a fundamental part of any house’s structure. Calculate the lumber needed for wall framing, considering the height, length, and number of walls in your 1500 sq ft house.
Roof Trusses
Roof trusses provide support for the roof and ceiling. The span of your house and the pitch of the roof will affect the number and size of trusses required.
Floor Joists
Floor joists support the flooring and provide stability to the structure. Calculate the number and size of floor joists based on the house’s layout and load-bearing requirements.
Beams and Posts
Beams and posts are essential for supporting heavy loads and creating open spaces within the house. Determine their size and quantity based on the architectural plans.
Choosing the Right Lumber
Softwood vs. Hardwood
Decide whether you will use softwood or hardwood for your construction project. Softwood is more commonly used for framing due to its affordability and availability.
Lumber Grades
Lumber comes in different grades, each with its quality and price point. Select the appropriate grade based on your budget and project requirements.
Accounting for Waste
Factor in Waste
It’s essential to account for waste when calculating lumber requirements. Typically, a 10% waste factor is added to the total lumber estimate to accommodate cutting errors and unforeseen issues.
Additional Considerations
Doors and Windows
Don’t forget to include the lumber needed for doors and windows in your calculations. These openings require framing and trim.
Exterior Siding
Consider the type of exterior siding you plan to use and calculate the lumber required for its installation.
Interior Finishes
Interior finishes such as drywall, trim, and flooring also require lumber. Include these in your overall lumber estimate.
Finding Quality Lumber Suppliers
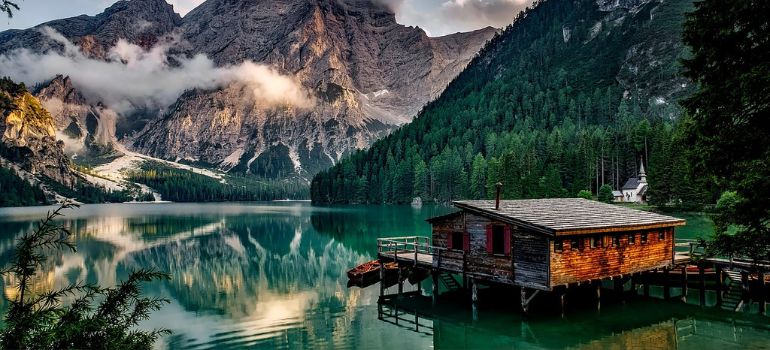
Research Local Suppliers
To ensure you get the best quality lumber for your construction project, research and identify reputable local lumber suppliers. Check reviews, ask for recommendations from other builders or contractors, and visit the supplier’s location if possible to inspect the lumber yourself.
Seek Sustainable Options
Consider using sustainable and eco-friendly lumber options if they align with your values and project goals. Lumber certified by organizations like the Forest Stewardship Council (FSC) ensures responsible forestry practices.
Managing Lumber Costs
Get Multiple Quotes
Don’t settle for the first lumber quote you receive. Get multiple quotes from different suppliers to compare prices and choose the most cost-effective option. Be sure to factor in the quality of the lumber and the supplier’s reputation.
Consider Bulk Purchases
If your project requires a substantial amount of lumber, inquire about bulk purchasing options. Many suppliers offer discounts for larger orders, which can help reduce overall costs.
Optimize Lumber Cutting
Work closely with your contractor or carpenter to optimize lumber cutting and minimize waste during the construction process. Efficient cutting and framing can significantly reduce the amount of lumber needed.
Reuse and Recycle
Explore opportunities to reuse or recycle lumber from other construction projects or salvage yards. Repurposing lumber can be both environmentally friendly and cost-effective.
Conclusion
In conclusion, determining how much lumber you need to build a 1500 sq ft house involves careful planning and consideration of various factors. Assessing your design, understanding local building codes, calculating lumber for framing, choosing the right lumber, and accounting for waste are all crucial steps in the process. By following these guidelines, you can ensure that your construction project runs smoothly and stays within budget.
Frequently Asked Questions
Without plans, you can still get a rough estimate by measuring the perimeter and height of the walls, and then consulting with a lumber supplier or contractor for guidance.
One common mistake is underestimating waste. Always include a waste factor in your calculations. Additionally, overlooking the need for doors, windows, and interior finishes can lead to inaccurate estimates.
Softwood is generally preferred for framing due to its cost-effectiveness and availability. Hardwood is often reserved for specific architectural features or interior finishes.
Yes, you can adjust the estimate if you make design changes, but it’s essential to consult with a professional to ensure accuracy and structural integrity.
You can find quality lumber at local lumberyards, home improvement stores, or through reputable online suppliers. Be sure to choose a supplier that offers the specific types and grades of lumber you need for your project.