Plasma cutters are the trailblazers when it comes to making intricate metal artworks or curving a metal sheet in the cleanest way.
Your oxyacetylene torch or centuries old welding machine simply cannot keep up with the precision and ease plasma cutters offer.
So, it is time you put those dated cutters back on the shelf and get the best plasma cutter on budget!
In this article, we are going to tell you about the many ways a plasma cutter will bring out the A game in your metalwork!
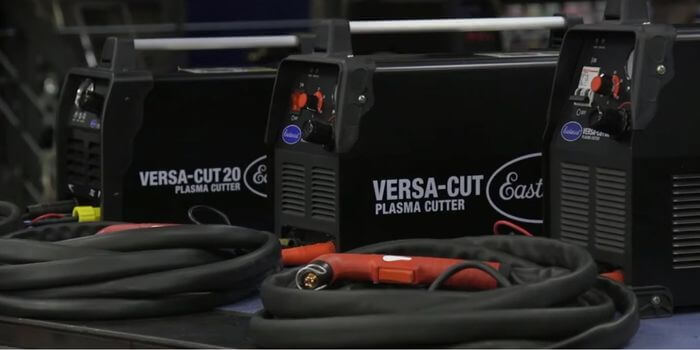
What is a Plasma Cutter?
If you think that a plasma cutter is a whirring needle making its way through a metal sheet like a tattoo gun, you’re wrong.
Although a handheld plasma cutter looks pretty harmless, it is able to cut through aluminium, stainless steel, steel, copper, titanium, brass, cast iron and other conductive alloys and metals of various thicknesses.Handheld plasma cutters are best if you have a metalworking hobby or run a small workshop.
However, computer-controlled CNC plasma cutters are for manufacturing, industrial or heavy construction works. Then again, there are some top-notch plasma torches that can do both!
Why Do I Need A Plasma Cutter?
Are you ready to talk about how gas welding is sucking the life out of you when you have a busy day at the workshop? Acetylene torches are the go-to cutters for most workers because they are cheap and everybody is using them.
But the fact that they are not suitable for some materials, and the cases in which they are, the warping at the edges due to heat is enough to make your heart sink.
So, if you have an upcoming metal project that requires greater accuracy, nothing but a plasma cutter will help your inner craftsmanship shine!
How Does a Plasma Cutter Work?
Using plasma in metalworking is the most efficient, safe and clean way to cut and curve metals. A plasma torch involves compressed gas such as oxygen, nitrogen, argon or shop air known as the “cutting gas” alongside a layer of “shielding gas” to protect the appliance from melting down.
When you turn the power switch on, an electric arc is sent through the cutting gas to elevate its temperature dramatically so as to reach a point where the gas becomes the fourth state of matter known as plasma.
This plasma stream is forced out of the nozzle at a superior speed with extreme precision. This is how plasma cutters produce a narrow kerf with minimum friction and heat dissipated across the whole sheet.
How Deep Does a Plasma Cutter Cut?
Distortion-free finishing and precision being the main selling points of a plasma cutter, there are other benefits such as slitting both ferrous and non-ferrous metals.
But the question remains- “How accurate is a plasma cutter?” and here we are with the answer!
You are never going to do a neat job with an acetylene torch on a chunky piece of metal because the thicker the metal, the rougher the edges are going to be.
Not only does it do damage to your project but it is also a tediously time-consuming task.
Handheld plasma cutters can make a 1.5inch deep cut on metals which goes up to a whopping 6inch cut when you have an industrial-strength CNC plasma torch!
How Precise is a Plasma Cutter?
Plasma cutters produce a smooth, cutting-edge finish like a laser; only at a more reasonable price! The only issue is that the ends are at a 4° to 5° slant since the plasma stream swirls through the material.
Instead of a straight cut, you get a slightly bevelled cut which is still far better than that of handheld hacksaws, circular saws or acetylene torches.
Most plasma cutters for hobby and home use will have a 10 to 45 amp output with a maximum cut that falls between the ¼ inch and ⅝ inch range.
Whereas professional grade plasma cutters will provide 50+ amp output, an outstanding duty cycle alongside a max cut of 1 inch or more.
CNC plasma cutters deliver a striking 150mm or 6 inch cut with an effective diameter around 50mm to 1500mm.
How to Choose the Best Plasma Cutter?
If you want the best plasma cutter on budget, you have to keep in mind how frequently you would be using the plasma torch or of what thickness your regular materials are going to be.
The accuracy of plasma cutters depends on a few things and we are listing them right below to help you out!
Cutting Speed
Even if you do not use a plasma cutter for your job, the cutting speed is still a crucial aspect because the slower the apparatus is, the more bevelled the end results will be. Do check the Inches Per Minute (IPM) denoting the plasma torch’s cutting speed.
Output Power
Choosing a 120 volt and 240 volt dual-voltage input gives a bang for your buck because plasma torches having this option tend to be an all-around device. They can nail both home use and creative metalworking.
You can get 60 amps of power from a 240 volt plasma torch for cutting ⅞ inch on most metals exceeding home necessity. In that case, 12 amps from a 120 volt plasma cutter will be enough for making a ⅛ inch slit.
Duty Cycle
Duty cycle is the length of time a plasma cutter can run simultaneously on your metal project without having to cool off.A greater timeframe or percentage indicates better functionality.
Lastly, a good air compressor and cooling system, output power, torch type, and cutting speed are the key attributes that help plasma cutters reach their highest accuracy.
Buy the Best Plasma Cutter on a Budget!
High-precision plasma cutters truly take the craft of metalworking up a notch. With a quality plasma cutter, you can flaunt your metalwork with the narrowest kerf.
The ones with greater precision will undoubtedly make all your metal items piece of the finest workmanship ever!